
Recovery of vanadium from black shale
LI Cun-xiong(李存兄), WEI Chang(魏 昶), DENG Zhi-gan(邓志敢), LI Min-ting(李旻廷), LI Xing-bin(李兴彬), FAN Gang(樊 刚)
College of Metallurgical and Energy Engineering, Kunming University of Science and Technology, Kunming 650093, China
Received 6 July 2009; accepted 30 December 2009
____________________________________________________________________________________________
Abstract: The recovery of vanadium from a black shale from Guizhou Province of China was performed using a three-step process, which consists of a leaching step in the H2SO4-HF-NaClO system under atmospheric pressure, the vanadium separation from leachate by solvent extraction and stripping, followed by precipitation of ammonium vanadate and thermal decomposition. Under the optimum leaching conditions of 100 g/L sulfuric, 15 g/L hydrofluoric acid, 1.5 g/L NaClO, 6 h leaching at 90 ℃ and oxygen partial pressure of 1 200 kPa, and the liquid-to-solid ratio of 2, about 91% vanadium extraction is achieved. The vanadium extraction yields of solvent and stripping are 99.83% and 97.66% when using 10% (volume fraction) P204, 5% TBP and 85% sulfonated berosene as organic phase and 15% (mass fraction) sulphuric acid as stripping agent. After thermal decomposition the purity of powder vanadium pentoxide products is 99.18% and the overall vanadium recovery is over 81% in the whole process.
Key words: black shale; vanadium extraction; H2SO4-HF-NaClO system; solvent extraction; precipitation; thermal decomposition
____________________________________________________________________________________________
1 Introduction
Vanadium is an essential trace element in the earth. With specific physiological functions, it is used extensively as an alloying element in steel and iron and titanium alloys, and as catalysts[1]. Even if vanadium widely distributes throughout the lithosphere, it is not present in high concentrations in minerals and the highest concentration of vanadium is found in shales and clays[2]. Usually, vanadium exists in the combination with various minerals which include carnotite, roscoelite, vanadinite, mottramite and patronite as important sources of the metal. Because of the low grade of vanadium in the processed ores and the depletion of concentrated ore deposits in the world, many industrial sub-products, including the converter and smelter slag[3-5], spent catalysts[6], and oil fly ash[7-14], are becoming interesting sources for the recovery of vanadium in industry.
In China, vanadium is mostly recovered from the converter and smelter slag produced by the treatment of titanomagnetites in iron and steel industry and black shale. Black shale is carbonaceous shale with several valuable metals, such as vanadium, nickel, molybdenum and silver. The common grade of vanadium in this ore is usually less than 2%. Black shale is the most important resource for vanadium extraction in China, which accounts for more than 87% of the domestic reserve of vanadium[15-16]. Conventionally, the recovery of vanadium from black shale was performed containing a preliminary roasting process, which emits serious poisonous gases of HCl and Cl2. With the increasing concerning of environment protection, the application of conventional technologies has been limited in China[17-20], and the classical process for vanadium recovery from black shale is gradually replaced by some environment friendly technologies[21-22].
The present work focuses on the design of integrated process for vanadium recovery from black shale. Firstly, the process is to systematically investigate the optimum conditions of vanadium extraction from one black shale in H2SO4-HF-NaClO system under atmospheric pressure, which gives the best yield of leaching and less pollution to environment. Secondly, to recover metal from the leachate, pretreatment of leach liquid and solvent extraction is involved. At last, purified vanadium pentoxide is prepared by precipitating the vanadium as ammonium vanadate and thermal decomposition.
2 Experimental
2.1 Materials
The experimental study was carried out using black shale from Guizhou Province of China. The composition of the black shale used in this study is listed in Table 1. Table 2 lists the mineralogical composition of the concentrate and valence distribution of vanadium in the sample. As listed in Table 1, the black shale sample has a relatively high vanadium content of 1.987% and high quartz concentration of over 53.03% by mass, and the concentrate is also characterized by high alumina fraction.
Table 1 Chemical composition of black shale (mass fraction, %)

Table 2 Mineralogical composition of black shale
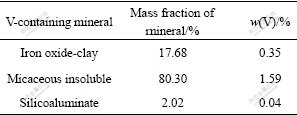
It can be seen from Table 2 that the main composition of the black shale are ferric oxides, kaoline, roscoelite and garnet. It is reported that V(Ⅲ) is substituted isomorphously with Al3+ in the roscoelite and garnet structure. V(Ⅳ) or V(V) compounds are weakly adsorbed to the ferric oxides and kaoline[16]. It can be seen from Table 3 that the distribution rate of V(Ⅲ) in the sample is about 34% and V(Ⅲ) is undissolvable in acid or alkaloid solution. So, NaClO is used as an oxidant in the present study to oxidize V(Ⅲ) into its dissolvable forms of V(Ⅳ) or V(V).
Table 3 Valence distribution of vanadium in black shale
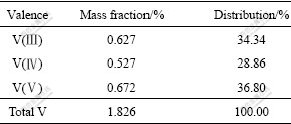
The particles less than 0.074 mm in the mineral sample used in this study account for 85%. The chemical agents, sulfuric acid, hydrofluoric acid, NaClO, NaOH, Na2SO3, NaClO3 and ammonia used in the present study are all of analytical grade. In all the leaching experiments we employed sulfuric acid and hydrofluoric acid as leaching agents and NaClO as the vanadium oxidating agents.
2.2 Procedures
The leaching and oxidation process were conducted at atmospheric pressure in a pyrex stirred reactor, equipped with a reflux condenser and placed in a heated water bath. The various solutions derived from leaching the black shale concentrate, precipitation of the ammonium vanadate, and washings of the cakes were separated by vacuum filtration. The leaching slurry was agitated at 550 r/min.
3 Results and discussion
3.1 Leaching
The main variables studied are the concentration of sulfuric acid and hydrofluoric acid in the leaching solution, the amount of NaClO oxidant to be employed, the liquid-to-solid ratio of the slurry, time, and the temperature of the reaction. The results obtained are shown in Figs.1-6.

Fig.1 Effect of sulfuric acid concentration on vanadium extraction (20 g/L hydrofluoric acid, 1 g/L NaClO, liquid-to- solid ratio 2, leaching time 6 h, temperature 90 ℃)
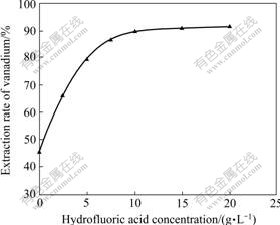
Fig.2 Effect of hydrofluoric acid concentration on vanadium extraction (100 g/L sulfuric acid, 1.0 g/L NaClO, liquid-to- solid ratio 2, leaching time 6 h, temperature 90 ℃)

Fig.3 Effect of addition of NaClO on vanadium extraction (100 g/L sulfuric acid, 15 g/L hydrofluoric acid, liquid-to-solid ratio 2, leaching time of 6 h, temperature 90 ℃)

Fig.4 Effect of liquid-to-solid ratio on vanadium extraction (100 g/L sulfuric acid, 15 g/L hydrofluoric acid, 1.5 g/L NaClO, leaching time 6 h, temperature 90 ℃)
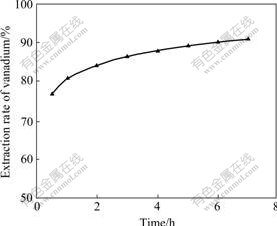
Fig.5 Effect of time on vanadium extraction (100 g/L sulfuric acid, 15 g/L hydrofluoric acid, 1.5 g/L NaClO, liquid-to-solid ratio 2, temperature 90 ℃)

Fig.6 Effect of temperature on vanadium extraction (100 g/L sulfuric acid, 15 g/L hydrofluoric acid, 1.5 g/L NaClO, liquid- to-solid ratio 2, leaching time 6 h)
It can be concluded from Figs.1-6 that the optimum conditions of the vanadium extraction from the black shale concentrate in the H2SO4-HF-NaClO system under atmospheric pressure are that the concentrations of leaching agent of sulfuric acid and hydrofluoric acid in the leaching solution are 100 g/L and 15 g/L, respectively, the amount of NaClO oxidant to be employed is 1.5 g/L, the liquid-to-solid ratio of the slurry is 2, leaching time is 6 h, and the temperature of reaction is 90 ℃. The experiments were carried out under the optimum conditions, the extraction rate of vanadium reaches about 91.2% and the composition of the leaching solution is shown in Table 4.
Table 4 Composition of leaching solution (g?L-1)
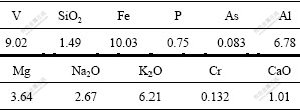
3.2 Solvent extraction and stripping
A series of experiments were carried out to determine the optimum extractants and extraction conditions, and di(2-ethylhexly)phosphoric acid (P204) and tributylphosphate (TBP) were chosen as extractants.
The organic phase was made up of 10% (volume fraction) P204, 5% TBP and 85% sulfonated kerosene. Before solvent extraction the leachate was adjusted to a suitable pH value of 2.0-2.5 using sodium hydroxide as neutralizing agent, and then followed by oxidizing any fraction of Fe(Ⅱ) to Fe(Ⅲ). An excess of 5% Na2SO3 was added compared to the total amount of Fe(Ⅱ).
After the pre-treatment, the leachate is free of Fe(Ⅱ). The organic phase, consisting of 10% P204, 5% TBP and 85% sulfonated kerosene, was used to extract vanadium in leaching liquor under the optimum conditions (obtained by our series of experiments) of pH 3.5, O/A ratio 1?6, ambient temperature for 10 min by six stages extraction. Stripping was performed by contacting the organic and 15% (mass fraction) sulfuric acid (O/A=6?1) at atmospheric temperature for 15 min. The results show that the solvent extraction and stripping of the vanadium are about 99.83% and 97.66%, respectively.
3.3 Precipitation and thermal decomposition
Whichever method (Ion exchange resins or solvent extraction) is used in separation of vanadium from leaching solution, the vanadium is finally precipitated as ammonium vanadate or vanadium pentoxide by ammonia or ammonium. The precipitation of the vanadium from the stripping solution was performed under the conditions that an excess of 25% NaClO3 was added compared to the total amount of vanadium as the vanadium oxidating agent (oxidation of V(Ⅳ) to V(Ⅴ)) at the boiling temperature of the solution, after 1 h of oxidation, 18% ammonia was added to keep the pH at 2. Under these conditions vanadium in stripping solution was gradually crystallized into ammonium vanadate. After solid liquid separation the red cake of ammonium vanadate was thermal decomposited at 550 ℃ for 2 h to produce qualified powder vanadium pentoxide. The precipitation yield of vanadium into ammonium vanadate reaches 98.36%, and the composition of the powder vanadium pentoxide is shown Table 5.
Table 5 Composition of powder vanadium pentoxide products (mass fraction, %)

4 Conclusions
1) The optimum conditions of vanadium extraction from the black shale concentrate in H2SO4-HF-NaClO system under atmospheric pressure are that the concentration of sulfuric acid is 100 g/L, the concentration of hydrofluoric acid is 15 g/L, the amount of NaClO oxidant employed is 1.5 g/L, the liquid-to-solid ratio of the slurry is 2, the leaching time is 6 h, and the temperature of reaction is 90 ℃. The extraction rate of vanadium is 91.2% under these conditions.
2) Vanadium can be effectively separated from leachate by solvent extraction with di(2-ethylhexly) phosphoric acid(P204) and tri-butyl-phosphate(TBP) as extractants, the solvent extraction yield and stripping yield are 99.83%, and 97.66%, respectively.
3) The purity of the powder vanadium pentoxide product is 99.18% and the overall vanadium recovery is above 81% in the whole process.
4) The proposed leaching, solvent extraction, precipitation and thermal decomposition steps give a feasible alternative for the processing of black shale concentrate with different vanadium contents.
References
[1] MOSKALYK R R, ALFANTAZI A M. Processing of vanadium: A review [J]. Minerals Engineering, 2003, 16(9): 793-805.
[2] NRIAGU J O. Vanadium in the environment (Part 1) [J]. Chemistry and Biochemistry, 1998, 5: 5-10.
[3] YANG Su-bo. Vanadium extraction and reclamation from converter slag containing vanadium [J]. Iron and Steel, 2005, 40(4): 72-75. (in Chinese)
[4] YANG Jing-ling, JIN Xin. A new way of recovering vanadium from iron vanadium slag [J]. Journal of Beijing University of Chemical Technology, 2007, 34(3): 254-257. (in Chinese)
[5] QIAN Qiang. Experimental study of neutralization of vanadium- bearing converter slag with waste titanium dioxide spent acid [J]. Iron and Steel, 2009(2): 22-28. (in Chinese)
[6] ZHANG P W, INOUE K, TSUYAMA H. Recovery of metal values from spent hydrodesulfurization catalysts by liquid–liquid extraction [J]. Energy and Fuels, 1995, 9: 231-239.
[7] AKITA T M, TAKEUCHI H. Recovery of vanadium and nickel in fly-ash from heavy oil [J]. Journal of Chemical Technology and Biotechnology, 1995, 62: 345-350.
[8] LOZANO L J, JUAN D. Solvent extraction of polyvanadates from sulphate solutions by primene 81R. Its application to the recovery of vanadium from spent sulphuric acid catalysts leaching solutions [J]. Solvent Extraction and Ion Exchange, 2001, 19: 659-676.
[9] TSAI M S. A study of the extraction of vanadium and nickel in oil-fired fly ash [J]. Resources, Conservation and Recycling, 1998, 22: 163-176.
[10] MIURA K, NOZAKI K, ISOMURA H, HASHIMOTO K, TODA Y. Recycling process of fly ash generated from oil burning [J]. Materials Transactions, 2001, 42: 2465-2471.
[11] JANOS M, WILDNEROVA L T. Leaching of metals from fly ashes in the presence of complexing agents [J]. Waste Management, 2002, 22: 783-789.
[12] HALL M L, LIVINGSTON W R. Fly ash quality, past, present and future, and the effects of ash on the development of novel products [J]. Journal of Chemical Technology and Biotechnology, 2002, 77: 234-239.
[13] MIURA K, NOZAKI K, ISOMURA H, HASHIMOTO K, TODA Y. Leaching and solvent extraction of vanadium ions using mixer-setllers for the recovery of the vanadium component in fly ash derived from oil burning [J]. Solvent Extraction Research and Development, 2001, 8: 205-214.
[14] NAVARROA R, GUZMANA J, SAUCEDOA I, REVILLAB J, GUILBAL E. Vanadium recovery from oil fly ash be leaching, precipitation and solvent extraction processes [J]. Waste Management, 2007, 27: 425-438.
[15] BIN Zhi-yong. Progress of the research on extraction of vanadium pentoxide from black shale and the market of the V2O5[J]. Hunan Nonferrous Metals, 2006, 22(1): 16-20. (in Chinese)
[16] XIAO Wen-ding. Mineralogy of black shale from Shanglin of Guangxi and vanadium extraction with hydrometallurgical process[J]. Nonferrous Metal, 2007, 59(13): 85-90. (in Chinese)
[17] CHANG Na, GU Zhao-lin, LI Yun. Leaching process investigation on vanadium extraction from black shale[J]. Inorganic Chemicals Industry, 2006, 38(7): 57-59. (in Chinese)
[18] HE Dong-sheng, FENG Qi-ming, ZHANG Guo-fan, OU Le-ming, LU Yi-ping. An environmentally-friendly technology of vanadium extraction from black shale[J]. Minerals Engineering, 2007, 20(12): 1184-1186. (in Chinese)
[19] CAI Jin-qiang. New technology of extraction vanadium from black shale [J]. Conservation and Utilization of Mineral Resources, 1993(5): 30-33. (in Chinese)
[20] QI Ming-jian. The status and prospects of vanadium leaching from black shale [J]. Hydrometallurgy of China, 1999, 72(4): 1-10. (in Chinese)
[21] WEI Chang, FAN Gang, LI Min-ting, DENG Zhi-gan. Study on main factors effect of extracting vanadium from black shale containing vanadium by acid leaching with oxygen pressure [J]. Chinese Journal of Rare Metals, 2007, 31(Special): 98-101. (in Chinese)
[22] LI Min-ting, WEI Chang, FAN Gang, DENG Zhi-gan. Pathbreaking experimentation study on extracting vanadium from black shale by acid leaching with oxygen pressure [J]. Chinese Journal of Rare Metals, 2007, 31(Special): 28-31. (in Chinese)
_________________________
Foundation item: Project(50874053) supported by the National Natural Science Foundation of China; Project(2007GA010) supported by the Science and Technology Bureau of Yunnan Province, China
Corresponding author: LI Cun-xiong; Tel/Fax: +86-871-5188819; E-mail: licunxiong@126.com
(Edited by LONG Huai-zhong)